There have been long-running discussions around the topic of renovating existing facilities, including the question of whether to demolish and rebuild or use the existing framework as a basis for creating a building that is more fit for purpose.
These conversations have received a boost as a result of the drive to achieve the UK’s legally-binding target of net zero carbon emissions by 2050, which has led to more facilities being considered for renovation. The principle aim of this is to reduce the levels of embodied carbon within the components used, but the reopening of the Black & White Building by The Office Group (TOG) in London’s Shoreditch area provides a highly relevant alternative view..
Those interested to read how facilities can include the extensive use of wood – one of the most sustainable materials available – to create a highly effective, healthy and attractive workplace are invited to hear more on this topic.
Waugh Thistleton Architects associate director David Lomax conducted an exclusive tour of the building for FM Director, explaining the overriding concept and its focus on sustainability throughout. “The building was previously used as a warehouse. TOG purchased the freehold with planning consent and painted the building black and white, which is where it gets its name. It became apparent that the current structure wasn’t fit for purpose so they used the site to construct a larger and much more sustainable workplace,” he explains.
“We’ve used wood for all aspects of the building above ground level, so there’s no concrete above ground and very few other materials,” Mr Lomax continues. “This means there’s significantly less embodied carbon when you compare wood with steel or concrete.” Although concrete has been used in the construction of the floors below ground level, it is entirely absent within the six floors and rooftop terrace of the new structure.
Explaining the decision to use timber throughout the facility, Mr Lomax stresses the importance of sourcing from suppliers that replant trees after they have been cut down, or allow them to regrow. In addition to its sustainability credentials, timber is also a highly attractive material, he says.
“Some buildings choose not to show their use of wood and hide it behind panels or paint over it, but we wanted it to be seen. Everyone likes to see woodgrain and it’s both comforting and restful, which is very supportive of the Black & White Building’s focus on health and wellbeing.”
The building is the first to be rebuilt in the TOG company’s 20-year history, with all others having been refurbished. Company co-founder Charlie Green says: “The Black & White Building represents a major step forward for us and – I hope – the wider industry too.
“It’s a statement of who we are and how we will approach sustainability; we don’t need to build the traditional way with concrete and steel anymore,” he says.
Using timber in place of these materials means that it was constructed with 37% less embodied carbon, the company states. In addition to its groundbreaking implications for TOG, the facility is also one of the highest mass-timber buildings in central London at 17.8m high, proving that the concept is entirely suited for contemporary offices and workplaces.
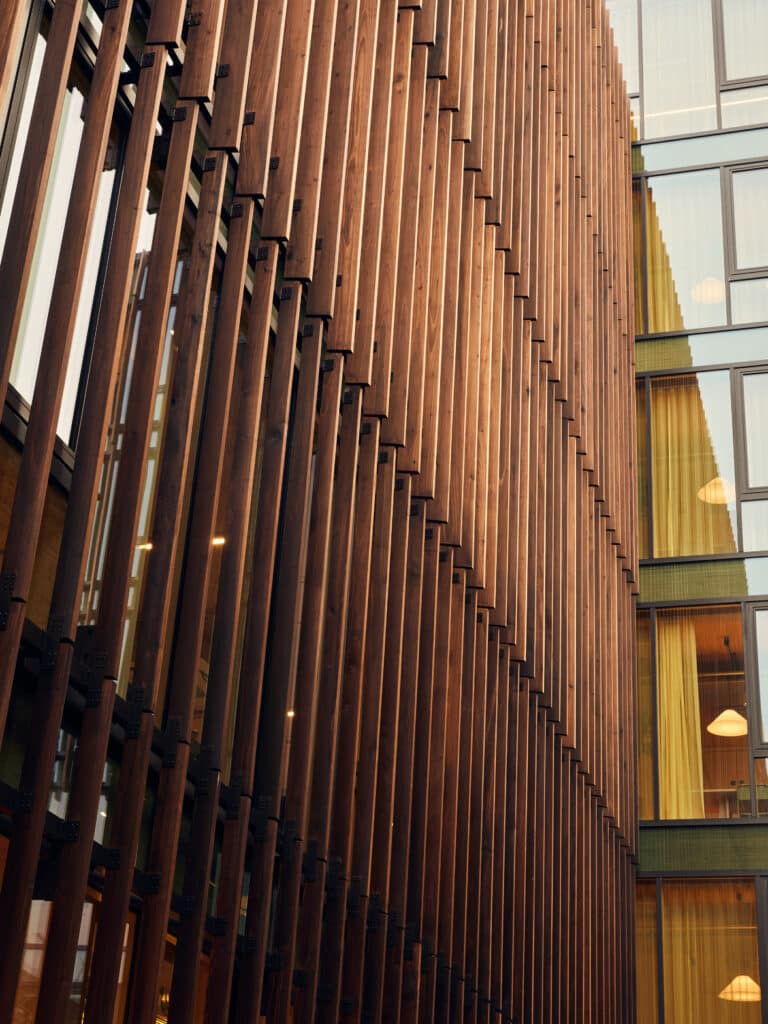
Mr Lomax further explains that instead of using concrete and steel to provide the central support for the building, this is delivered by cross-laminated timber (CLT) panels and laminated veneer lumber (LVL) columns and beams sourced from Germany. “The columns are made from hardwood and are loadbearing, taking up less space than a concrete – or softwood – alternative and they’re 2.9 times stronger than steel,” he says.
Another relevant detail is the use of wooden plugs throughout the building to fix the beams and other wooden panels and avoid the use of metal-based alternatives. In addition to CLT, Mr Lomax and his team included laminated veneer lumber (LVL) beams, which also provide high levels of support to the structure.
Both CLT and LVL weigh considerably less than concrete or steel and therefore require lower levels of energy to transport and install, further increasing their sustainability credentials. Natural materials are additionally easier to maintain and recycle at the end of the building’s life.
High levels of daylight are provided by floor-to-ceiling glazing in many areas, with 57% of the exterior walls consisting of glazing. Having mapped the solar path, Tulipwood louvres have been fitted to the south-facing exterior to reduce solar gain and optimise the flow of natural light and heat into the building.
“The louvres are made from hardwood, because this is obviously more durable than softwood, and are sized so that they provide more shade at the top of the building, which will receive more sunlight, and gradually reduce in depth for lower floors. We designed the building from the inside outward using the architectural sufficiency model,” he continues.
“We also considered the future changes that may be required and we’ve made sure that flexibility has also been included. You never know exactly what will be required but you can design a building so that its internal layout can be altered with the minimum of fuss.”
This means that partition walls or room dividers can be easily installed or removed to meet the requirements of individual leaseholders and allow them to adjust their surroundings to meet the changing needs of their businesses.
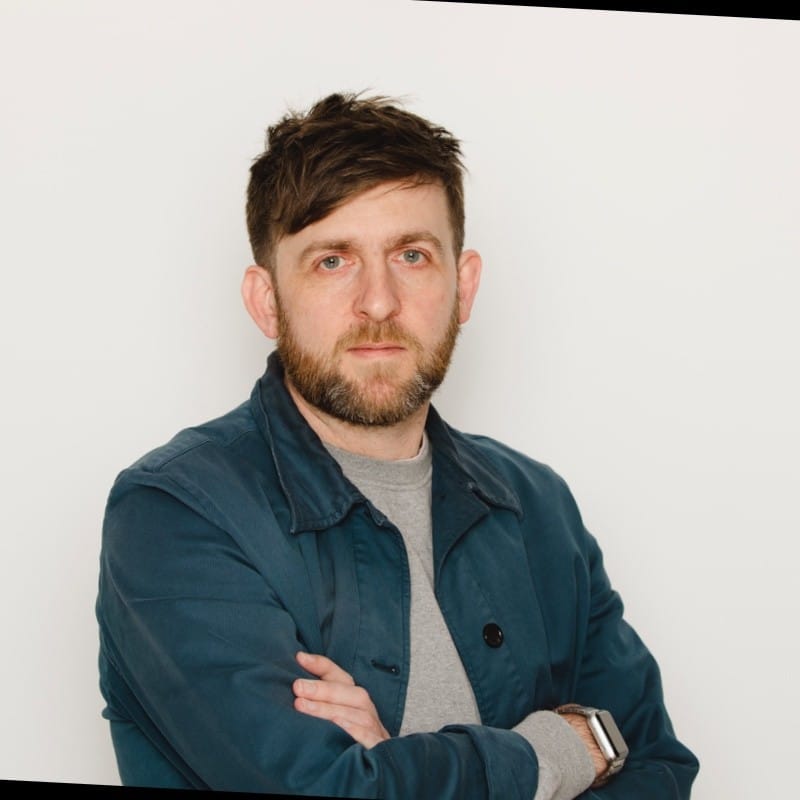
Mr Lomax also states that obtaining insurance was not an insurmountable barrier for the Black & White Building and points out that wooden beams perform better than steel alternatives during a fire. “Steel will get to the point where it collapses due to the heat in a major fire, but wood will become charred on the outside while remaining structurally supportive if carefully designed by a competent team.
“So in the case of insurance, it’s just a case of knowing how to collaborate with risk assessors to explain the benefits of wood to emphasise its strength in all areas,” he says.
Perhaps one of the most important aspects is to ensure the full support of the building owner is included in all stages for the successful design of a sustainable building, Mr Lomax continues. “It’s absolutely essential to have a fully engaged client and TOG were exactly that, so they deserve a lot of credit for their vision and support for this project.”
Another benefit of the extensive use of timber can be seen in that the Black & White Building’s construction was completed in just 14 weeks and required a mere six to eight people. Mr Lomax provides the example of electricians found in a local park after finishing earlier than anticipated, due to the ease with which wiring and cable mountings had been fitted into the wood panels.
“It was quick and quiet and we had no complaints about noise or dust. There’s no need to use anything heavier than a hand-held drill to install cables and other fittings, which also means it’s very easy to move these if any changes are needed to the internal layout in future,” he says.
Increasing the roof space of the building has allowed 200 sq m of solar panels to be installed to support the air-source heat pump and TOG’s desire for renewable energy to contribute to the building’s energy requirements, with a total of 26.1% of the building’s predicted energy use coming from these sources. The facility has been accredited as BREEAM Excellent and provides further proof of the successful outcome of the project.
Where heating and cooling of the new building is concerned, Mr Lomax states: “all tenants are informed that they have heating and cooling available and are educated to make sensible decisions, and that means they turn these off if they open a window, for example. The use of wood also means that indoor air quality is better than if we’d used gypsum panels or concrete.”.
He further explains that the extensive use of timber has significant additional benefits in areas such as acoustics and indoor aroma. He adds that the design of the facility incorporates many of the features that are now considered essential to encourage interaction and collaboration between colleagues.
These include breakout and informal meeting areas on all floors of the building, utilising both indoor and outdoor space, with the roof of the facility used as a terrace that features extensive use of timber.
Having reached the practical completion stage with Waugh Thistleton Architects, TOG engaged the services of local design studio Daytrip to develop an interior design that matches the building’s exterior. As a result, kitchen surfaces including recycled paper composite boards and corridors lined with Viroc particle boards in dappled ochre blend with the exposed timber in all areas.
Interior fittings and furniture have also been sourced with sustainability as the most important factor, with seating and tables using wood as a main component and deep-pile fabrics for upholstered chairs and sofas. Bearing in mind all the information above, it will not be surprising to learn that recycled and locally-sourced materials make up a significant percentage of those used.
There is a long list of positive elements already embedded within the new Black & White Building and these have considerable potential to be further extended in the future. With both the building owner and architect stating their conviction that the building can serve as a model to inspire and encourage others to raise their sustainability efforts, it further supports the view that the adoption of this attitude can significantly reduce carbon emissions over the course of many years into the future without including additional financial outlay.
The final word goes to Mr Green who says: “We’ve always been committed to having a strong sustainability agenda. Throughout the portfolio, we have a number of green roofs giving thermal performance, bio-diversity and storm water run-off protection, rainwater harvesting, grey water recycling, solar and PV panels and we work hard to use recycled and recyclable materials across all of our buildings.
“The original B & W building was deteriorating rapidly, so our normal approach of refurbishing was not possible. So we looked to develop a new build with a construction methodology that would push the boundaries.
“Timber was the obvious route to reduce the embodied carbon as much as possible. But this building is all timber above ground, with timber beams and columns made from beech (LVL) as opposed to steel and a full timber core rather than concrete,” Mr Green concludes.
Black & White Building’s BMS
Environmental Engineering Partnership director Neil Reynolds states that the building has a full BMS system providing automatic time and temperature control for all its mechanical systems.
“The BMS also monitors energy usage by system, including lighting, small power and power used for heating, cooling and ventilation systems. The system also monitors PV energy generated. This energy usage data is stored and can be reviewed for set periods of time and be used for benchmarking, both against predicted energy usage and against other buildings in the portfolio,” he continues.
The BMS is used to remotely monitor alarms and provide an early warning status where system inefficiencies occur, including leak detection systems to avoid water wastage or damage to the building should a leak occur. Heating and cooling in occupied areas of the building are time-controlled and will remain off should the office space be empty.
“Lighting within offices is fully automatic once switched on. Absence detection in the space switches the lighting off when there is no movement, or the space is empty. Switches in each space allow the clients to switch off the lights manually should daylight be sufficient,” says Mr Reynolds.