Clockwork Removals and Storage has over 25 years’ experience in the provision of commercial relocations and move management services
With a network of seven branches throughout the UK, its experienced commercial team works across both the public and private sectors. The company believes a successful relocation should be delivered on time and within budget, while minimising down time and disruption to its clients.
Clockwork finds that the office environment is continuing to adapt to the post-Covid environment and it is assisting its clients with reconfiguring their workspace to ensure a smooth, efficient and safe return of their staff to their workplace.
Certificate of excellence
Recently awarded the British Association of Removals (BAR) Commercial Moving Group’s certificate of Excellence for 2022, Clockwork also has the Safe Contractor accreditation, ISO 45001 in occupational health and safety, and holds the ISO 9001 in quality management.
It is focused on its environmental impact and ISO14001 environmental management systems certification and all vehicles are fully compliant with the UK’s Ultra Low Emission Zones (ULEZ). The business also engages with tree planting and carbon capture schemes, while ensuring that the materials it uses are recycled and/or recyclable.
Two examples of recently completed projects include the relocation of the Macdonald Hotel Group.
The Clockwork team conducted an extensive relocation for the Oxford-based hotel, which is part of a nationwide group. It had recently been sold and required all the furniture in the bedrooms and public rooms to be delivered to three different hotels in the group for storage.
The large relocation project was conducted over 11 days, with a total of 17 crew, eight vehicles and a highly experienced move manager. Over 100 boxes were needed as well as 20 roll cages for delicate light fittings, oversized mirrors and countless glass covers for bedside cabinets.
All fragile items were treated with the utmost care, expertly packed and wrapped by the team for transit and storage. A high number of beds had to be moved, including several oversized four posters. These could not fit in the small residential lift, so the crews carried them down the sweeping staircases.
This relocation posed logistical difficulties, including large numbers of very similar-looking furniture having to be delivered to specific locations throughout the UK. Despite the potentially high margin for error the company’s crew and its experienced move manager made sure the hotel relocation went without a hitch.
The next case study was for a laboratory, whose Edinburgh branch relocated a range of freezers, hoods, large cabinets and specialist laboratory equipment.
The operation was highly complex and completed by a team of six operational staff using ramped and tail lift vehicles. The team also needed nearly 100 specialist crates along with appropriate lifting equipment.
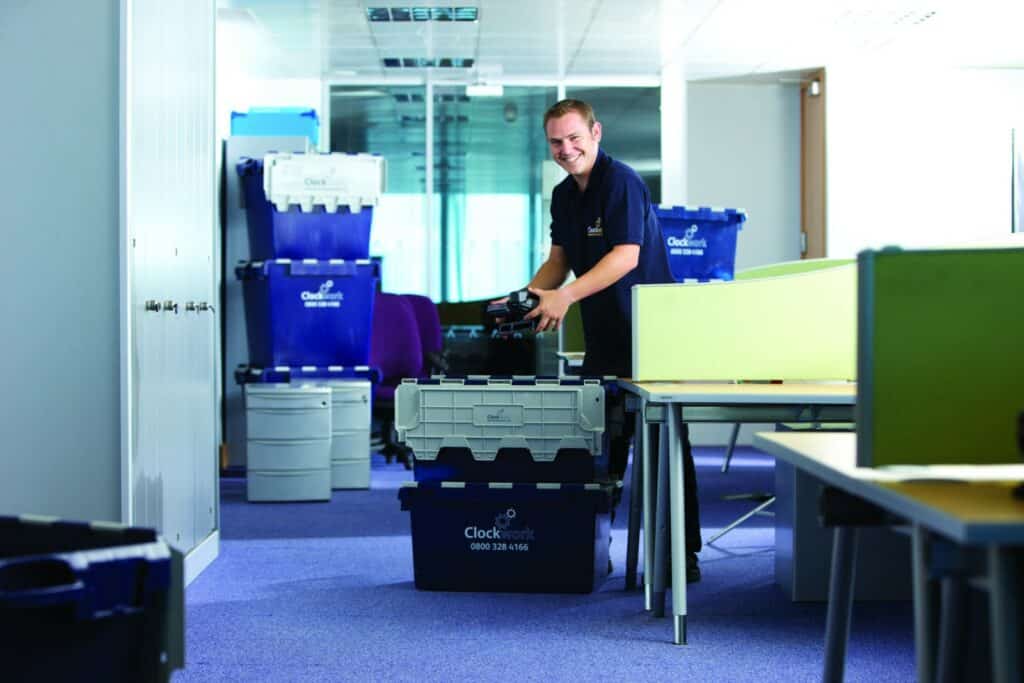
Further analysis
Following initial risk assessments, walkways and equipment was made safe for the removal. Correx and floor protection were used to safeguard the lift and walkways. The crew packed the equipment into the crates using bubble blankets and paper for each item.
IT equipment was protected with specialist monitor covers and then secured into larger IT crates and the use of specialist removals equipment to navigate through the building and onto the ramped lorry.
A team of four operational staff then set about moving the large hoods and cabinets, whilst the two most experienced packers packed the contents of the freezers. The freezers were then moved by the entire team, using specialist equipment to ensure they remained stable and upright.
A risk assessment was completed prior to work starting at the new location, with several areas again protected with Correx. The crates were then delivered from the ramped vehicles and the freezers were carefully moved to their new location.
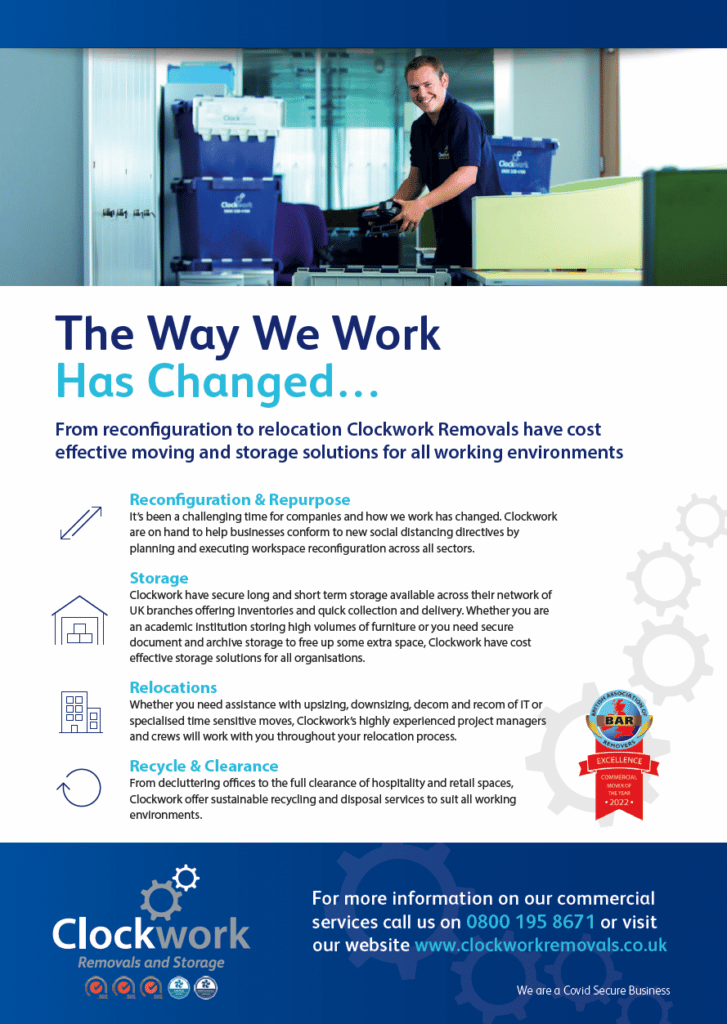